The electric hub motor I purchased had a set of six holes built in for adding a 140mm disk brake rotor. Unfortunately, the bike frame I had used was not set up to mount a disk brake caliper.
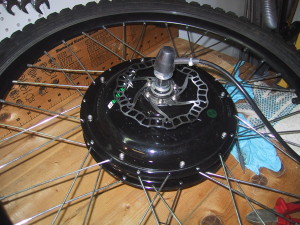
I purchased the cheapest cable actuated disk brake caliper and rotor set I could find on ebay ($50) and then had to figure out how to mount the caliper. After a bit of thought, I eventually decided to keep it classy and not weld the entire thing directly to the bike frame.
Disk brake calipers are mounted using two screws, hopefully with lock washers to make sure they don’t come out. M6 SHCS (Socket Head Cap Screw), typically 1.0 thread pitch and 18mm long)
Although my bike frame did not have built-in holes for a disk brake caliper, it did have some threaded M6 holes for other purposes (racks/mudguards, etc..), so I could use one of those, and only had to add a 2nd mounting hole at exactly the right place.
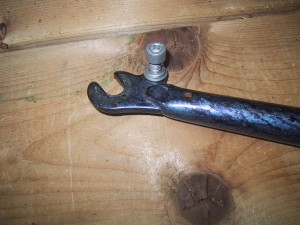
From chopping apart a lot of bike frames, I had some spare steel, and one of the spare front forks also had an M6 hole tapped into it, so I didn’t even have to drill and tap the 2nd hole. I used a cut-off wheel on an angle grinder to liberate the hole and surrounding steel, then screwed it to the 2nd hole in the caliper, using the caliper body itself to hold the steel piece in place while I welded it. (The caliper also has two screws that adjust the body slightly, so the weld doesn’t have to be 100% perfect…)
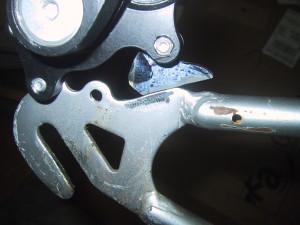
Getting the small piece of steel, and cleaning off all the excess paint to get the parts ready to weld took a lot longer than actually doing the small weld. (I could have brazed the two together, but since I have the welder just sitting there, and the welded joint will be stronger, always important for brakes…)
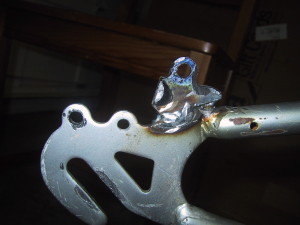
Of course, because the brake caliper itself has M6 threaded holes, you don’t want the holes on the frame to ALSO be threaded (because then you can’t use the screws to tighten the caliper to the frame of the bike effectively) so after I had the holes positioned where I wanted them, I used a drill bit to ream the threads out of the holes on the frame. (N.B….never use a drill bit as a reamer…unless you don’t have a reamer….)